Ultimate Overview to DTF Printing Techniques for Magnificent Fabric Styles
Beginning on the trip of mastering DTF printing methods can open up a world of opportunities for producing visually exciting textile layouts. In this overview, we will certainly explore the intricate information of DTF printing, from realizing the essential essentials to unraveling advanced shade methods that can elevate your styles to new heights.
Understanding DTF Printing Basics
DTF printing, a procedure that includes moving designs from a special movie to textiles utilizing warmth and pressure, develops the structure of fabric printing strategies. This ingenious method permits high-quality, dynamic layouts to be effortlessly transferred onto different materials with accuracy and information. The initial step in DTF printing involves developing or selecting a layout that will be published onto the textile. This layout is then published onto a special film making use of a DTF printer, which utilizes specific dyes or pigments to make sure color precision and sturdiness.
The final result is a stunning, lasting textile style that is washable, versatile, and resistant to fading. In general, understanding the basics of DTF printing is vital for grasping this contemporary textile printing technique.
Choosing the Right Textile Products
Having actually developed the fundamental concepts of DTF printing methods for textile styles, the next crucial consideration lies in selecting the appropriate fabric products to match this ingenious process efficiently. The success of a DTF print largely depends on the compatibility in between the chosen fabric and the printing technique. When choosing textile materials for DTF printing, it is necessary to think about the material's structure, weave, and texture. Fabrics that work well with DTF printing consist of polyester blends, spandex, nylon, and various other synthetic products. These materials normally have a smooth surface that enables vivid and thorough prints. Additionally, the stretchability of these products can accommodate the heat transfer procedure associated with DTF printing without distorting the design. It is suggested to prevent natural fibers such as cotton or silk, as they may not yield the same level of print quality and longevity. By picking the ideal fabric products, designers can make best use of the capacity of DTF printing to produce durable and sensational textile designs.

Mastering the Printing Process
To succeed in DTF printing methods for fabric layouts, mastering the printing process is necessary for attaining consistent and premium results. The printing process in DTF includes a number of crucial actions that call for accuracy and focus to information. Preparing the art work for printing is essential. This includes making sure the style is appropriately sized and placed for the fabric. Next off, the design is printed onto a special DTF film utilizing a compatible printer with the ideal setups to accomplish ideal shade vibrancy and clearness (DTF Printing). When the style is printed, it is then transferred onto the fabric making use of a heat press machine. The temperature, stress, and period of heat application must be carefully managed to make sure appropriate adhesion of the layout to the fabric. Furthermore, grasping the peeling procedure after warmth pressing is important to avoid any damage to the layout or material. By refining each of these steps in the printing procedure, developers can constantly produce sturdy and sensational textile layouts with DTF printing methods.
Enhancing Styles With Color Methods
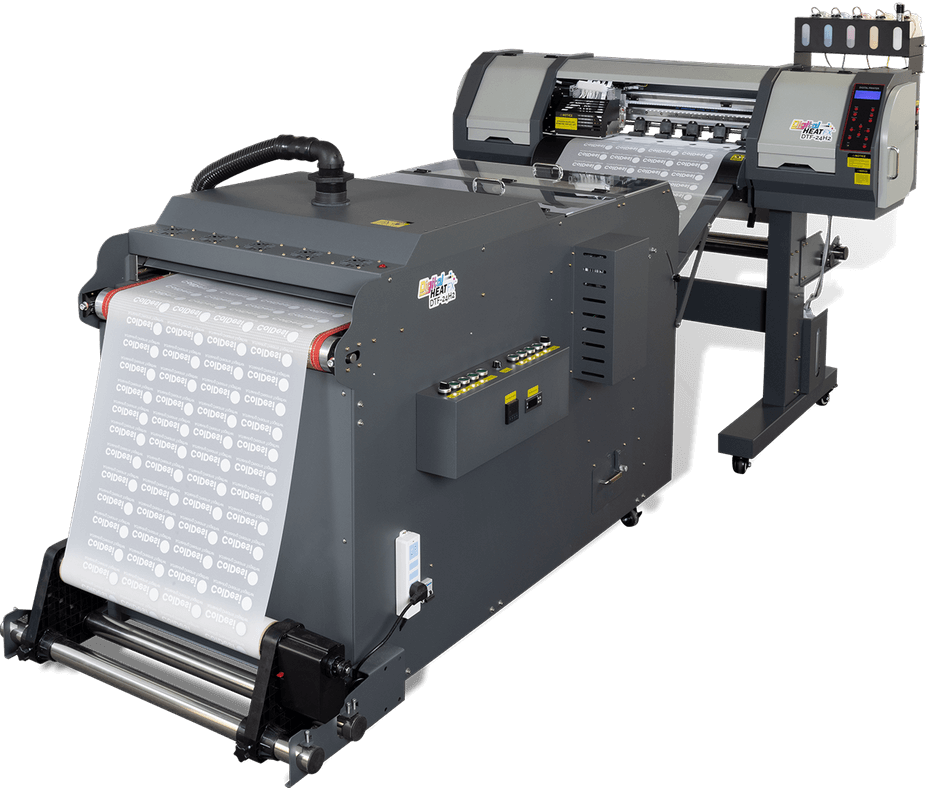
Furthermore, trying out color gradients can bring a sense of motion and fluidness to the layout. By mixing shades seamlessly, a gradient effect can be achieved, including a vibrant and modern-day touch to the fabric style. Furthermore, using color blocking techniques can develop striking and vibrant visuals by comparing various solid colors in distinct areas of the layout.
In addition, including metallic or neon colors can give a one-of-a-kind and eye-catching aspect to the textile layout, making it attract attention and emanate a sense of vibrancy. When strategically used, these color techniques can boost the general aesthetic allure of textile designs, making them extra memorable and exciting.
Troubleshooting Common DTF Printing Issues
After exploring different useful content color methods to enhance fabric designs, it is crucial to deal with usual DTF printing problems that might occur throughout the production procedure. One common problem is inadequate bond, which can arise from improper treating temperature levels or times. To settle this problem, make certain that the curing setups are accurate which the glue used appropriates for the certain material being published on. An additional constant challenge is shade incongruities, where colors may show up differently than expected. This can be brought on by incorrect color accounts or setups in the printing software. To tackle this, confirm the shade setups and accounts to ensure they match the designated style. In addition, issues with picture quality and intensity can occur due to low-resolution pictures or inappropriate printing techniques. To address this, constantly use top notch images and visit this web-site change the printing settings for optimum clearness. By understanding these usual problems and implementing the needed troubleshooting steps, you can boost the overall quality of your DTF printed fabric styles.
Final Thought
In conclusion, grasping DTF printing techniques is necessary for creating magnificent textile styles. With practice and interest to detail, one can produce distinct and attractive textile layouts utilizing DTF printing strategies.
Styles))))
DTF printing, a procedure that involves moving designs from a special movie to textiles utilizing warmth and pressure, develops the structure of textile printing methods.Having actually established the fundamental concepts of DTF printing techniques for fabric layouts, the next important consideration exists in selecting the proper fabric products to enhance this innovative process successfully. By picking the right textile materials, designers can optimize the possibility of DTF printing to develop stunning and resilient textile designs.
To stand out in DTF printing methods for fabric layouts, understanding the printing procedure is essential for achieving high-grade and regular outcomes. DTF Printing. By sharpening each of these actions in the printing procedure, developers can constantly produce magnificent and durable textile styles with DTF printing methods
Comments on “DTF Printing Revolution: Unleashing Creativity in Textile Design and Manufacturing”